The Ultimate Guide to Prototype Mold in Metal Fabrication
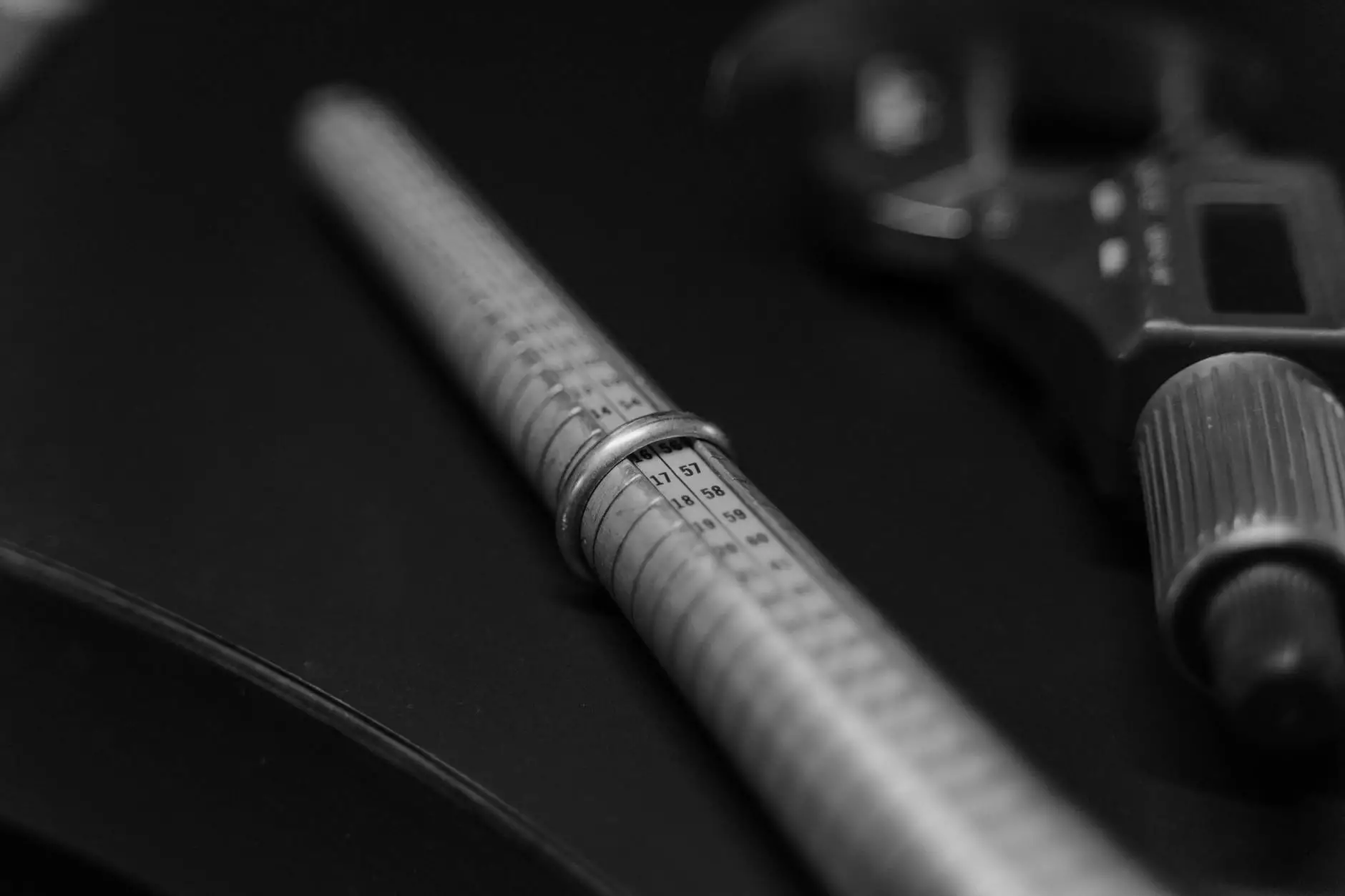
Understanding Prototype Mold
In the ever-evolving world of technology and manufacturing, the term prototype mold holds profound significance. A prototype mold serves as a crucial component in the product development process, allowing businesses to refine their designs and ensure precision before full-scale production.
At DeepMould.net, we specialize in metal fabrication, leveraging advanced techniques and technologies to create top-quality prototype molds. In this comprehensive guide, we will uncover the intricacies of prototype molds, their applications, and how they can positively impact your business.
What is a Prototype Mold?
A prototype mold is a custom-made mold used to create a prototype of a specific design. It allows manufacturers to produce test parts in order to evaluate the design’s feasibility, functionality, and aesthetic appeal. Typically, prototype molds are made from materials such as:
- Aluminum: Lightweight and cost-effective, ideal for low-volume production.
- Steel: More durable and better suited for high-volume production runs.
- Silicone: Used for softer, non-structural components where flexibility is needed.
Significance of Prototype Molds in Business
The use of prototype molds in business is paramount for several reasons:
- Cost Efficiency: Creating a prototype mold before full production can prevent costly mistakes and reduce waste.
- Quality Assurance: Allows for testing and validation of designs, ensuring that the final product meets required specifications.
- Time Savings: Speeds up the development process by allowing for adjustments before mass production begins.
- Improved Communication: Prototypes facilitate clear visual communication among team members and stakeholders.
The Prototype Mold Process
Understanding the process of creating a prototype mold is essential for businesses looking to innovate. Here’s a detailed walkthrough of the typical stages:
1. Design Phase
The journey begins with a concept or idea. Engineers and designers collaborate using CAD (Computer-Aided Design) software to create a detailed 3D model of the product. This model serves as the blueprint for the mold.
2. Mold Fabrication
Once the design is approved, the next step is fabricating the mold. This involves:
- Material Selection: Choosing the appropriate material based on functionality and production volume.
- Machining: Using CNC (Computer Numerical Control) machines to precisely shape the mold components.
- Assembly: Putting together the mold parts, ensuring accurate alignment and fit.
3. Prototype Production
With the mold ready, it is time to produce the prototype. This involves injecting or pouring materials into the mold and allowing them to cure or solidify. Common materials include various plastics or metals, depending on the application.
4. Testing and Evaluation
After the prototype is created, it undergoes rigorous testing. Engineers assess functionality, appearance, and performance. Feedback from these evaluations is crucial for making adjustments to the design or mold.
5. Iteration
The iterative process repeats as needed until the final product design meets all necessary criteria. This may require several rounds of prototyping and testing, ensuring that the final mold can produce parts that meet quality standards.
Applications of Prototype Molds
Prototype molds find applications across a myriad of industries:
- Aerospace: High-precision parts for aircraft and spacecraft.
- Automotive: Components for vehicles, focusing on performance and safety.
- Medical: Devices and tools that require strict adherence to safety and efficacy standards.
- Consumer Electronics: Enclosures and internal components for electronic gadgets.
Benefits of Using Prototype Molds
By incorporating prototype molds into their development processes, businesses can enjoy numerous benefits:
Enhanced Product Quality
Because prototype molds allow for testing and validation, the final products tend to exhibit higher quality and reliability.
Faster Time-to-Market
The ability to iterate quickly through prototyping means organizations can launch products faster, gaining a competitive advantage in the market.
Risk Mitigation
Testing designs thoroughly with prototype molds reduces the risk of failures and recalls, safeguarding investments and brand reputation.
Customizability
Businesses can create customized molds that cater to unique needs, resulting in products that better meet customer requirements.
Choosing the Right Partner for Prototype Mold Fabrication
Selecting a reliable partner for prototype mold fabrication is crucial. At DeepMould.net, we prioritize quality, precision, and customer satisfaction. Here are some factors to consider when choosing a partner:
- Experience: Ensure the company has a proven track record in fabricating molds specific to your industry.
- Technology: Look for advanced manufacturing technologies that enhance efficiency and accuracy.
- Customer Support: A good partner will offer comprehensive support throughout the development process.
- Quality Assurance: Evaluate their quality control processes to ensure high standards are maintained at every stage.
Future Trends in Prototype Mold Technology
As technology advances, the future of prototype molds is set to evolve dramatically. Here are some trends to watch:
1. Additive Manufacturing
The rise of 3D printing technology is reshaping how molds are created. It allows for rapid prototyping and the production of complex geometries that traditional methods might struggle to achieve.
2. Smart Manufacturing
Incorporating IoT (Internet of Things) devices in mold fabrication can enhance monitoring and control, ensuring optimal conditions throughout the production process.
3. Sustainable Practices
As environmental concerns continue to rise, the industry is moving towards sustainable practices in mold manufacturing, including the use of recyclable materials and reducing waste.
Conclusion
Investing in prototype molds is an essential step for businesses in the metal fabrication industry looking to innovate and improve their product offerings. By embracing advanced mold manufacturing techniques and understanding the benefits of prototypes, companies can significantly enhance product quality, speed up their time-to-market, and mitigate risks.
At DeepMould.net, we are committed to providing unparalleled expertise in metal fabrication and mold-making processes. Partner with us to transform your ideas into reality and drive your business forward.