The Essential Guide to Industrial Concrete Mixers
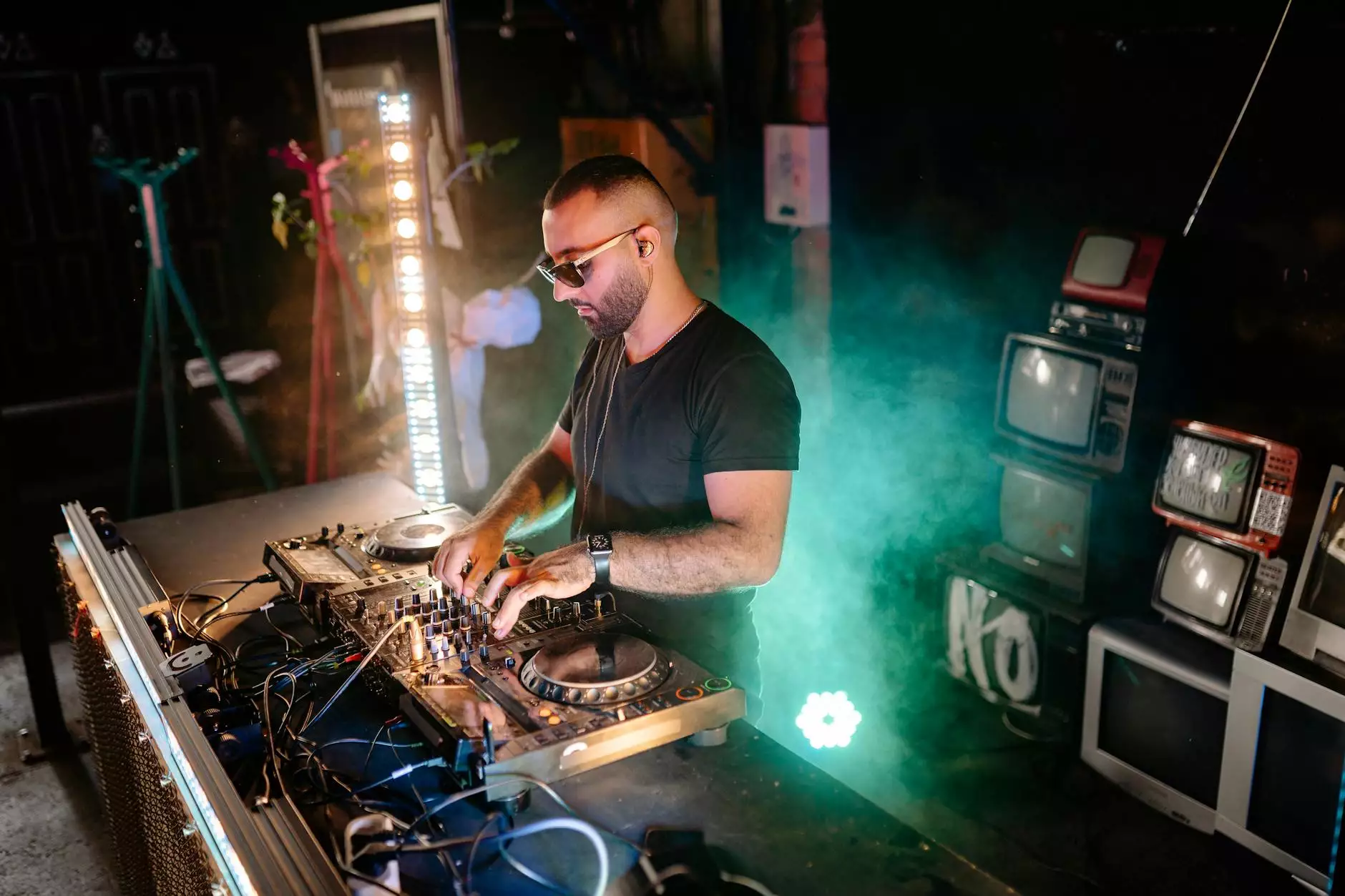
Industrial concrete mixers play a pivotal role in the construction industry, streamlining processes and enhancing productivity on job sites. They are indispensable for mixing and blending components necessary for creating concrete, which is a backbone material in various constructions, from residential buildings to massive infrastructure projects.
The Importance of Industrial Concrete Mixers
Understanding the significance of industrial concrete mixers involves recognizing the vital role concrete plays in the construction industry. Concrete is widely used due to its durability, strength, and versatility. However, the effectiveness of concrete is heavily contingent upon the mixing process, which is where industrial concrete mixers come into the picture.
Evolution of Concrete Mixing
The evolution of concrete mixing has seen a shift from manual mixing techniques to advanced mechanical solutions. Early methods relied heavily on human labor, risking inconsistencies and inefficiencies:
- Manual Mixing: This was a labor-intensive process with a high chance of inaccuracies.
- Batch Mixers: Introducing batch mixers allowed for better consistency and quality control.
- Continuous Mixers: These further enhanced efficiency by keeping a constant flow of concrete.
How Industrial Concrete Mixers Work
Industrial concrete mixers function by thoroughly combining water, aggregate materials (like sand and gravel), and cement to produce concrete. The process can be broken down into several essential steps:
1. Ingredient Selection
The first step involves selecting quality ingredients. The durability and strength of the resulting concrete depend on the quality of the cement and aggregates used.
2. Measurement
Accurate measurement of the ingredients is crucial. This is where modern industrial mixers excel. They often come equipped with automated systems that ensure precise ratios of materials, thereby enhancing the quality of the mixture.
3. Mixing
Once the ingredients are prepared, they are placed into the mixer. The mixing process varies based on the type of mixer used:
- Drum Mixers: These utilize a rotating drum to blend the components.
- Sic Mixers: Known for producing high-quality mixtures, they mix materials more thoroughly.
- Planetary Mixers: These mixers achieve exceptional mixing results due to their unique design.
4. Discharge
After mixing, the concrete is discharged into a truck or directly onto the job site. Rapid discharge is crucial to prevent the mixture from beginning to set too early.
Types of Industrial Concrete Mixers
There is a variety of industrial concrete mixers available, each suited for different types of projects. Here’s a closer look at some common types:
1. Batch Mixers
Batch mixers are used for small to medium-sized construction sites. They work in batches, mixing a set amount of concrete at a time, which is ideal for projects that require specific concrete grades.
2. Continuous Mixers
Continuous mixers are engineered for large-scale projects. They can produce concrete continuously, which is vital for large pours such as roads or bridges, ensuring a steady supply of concrete with minimal downtime.
3. Twin-Shaft Mixers
Twin-shaft mixers are renowned for their efficiency and speed. They are commonly used in precast concrete applications, offering short mixing times and excellent homogeneity.
Benefits of Using Industrial Concrete Mixers
The adoption of industrial concrete mixers comes with numerous advantages that contribute to the success of construction projects:
- Increased Efficiency: These mixers significantly cut down the time required for mixing concrete.
- Enhanced Quality: Automated mixing leads to consistent and repeatable results.
- Cost Savings: By minimizing waste and optimizing material use, businesses can achieve substantial cost savings.
- Versatility: They can be used in a variety of projects, from small residential builds to large commercial sites.
Impact of Industrial Concrete Mixers on Sustainability
As industries strive towards sustainability, industrial concrete mixers contribute significantly by optimizing material use and reducing waste. Here’s how:
1. Efficient Material Use
By providing precise measurements and thorough mixing, these mixers ensure that the exact amount of materials is used, reducing surplus and waste.
2. Use of Recycled Materials
Modern mixers are capable of integrating recycled materials into the concrete mix. This practice not only lessens environmental impact but also promotes sustainability in construction.
Choosing the Right Industrial Concrete Mixer
When selecting an industrial concrete mixer, there are several factors to consider:
1. Project Requirements
Evaluate the size and scale of your project. Smaller projects might benefit from batch mixers, while larger developments could necessitate continuous mixers.
2. Type of Concrete
Different mixers are specialized for various types of concrete. Understanding the specific concrete grade required will assist in selecting the appropriate mixer.
3. Budget
Industrial mixers vary widely in price. It’s essential to balance cost with quality and capability to find the best fit for your needs.
Conclusion
In conclusion, the significance of industrial concrete mixers cannot be overstated in the realm of construction. They are at the heart of the concrete production process, ensuring efficiency, quality, and sustainability in construction practices. By understanding their operation, types, and benefits, businesses can make informed decisions that enhance productivity and contribute positively to project outcomes.
As the industry continues to evolve with new technologies and methodologies, the role of concrete mixers will undoubtedly adapt, paving the way for advancements in construction efficiency and quality. Invest in the right industrial concrete mixer today, and experience the difference it can bring to your next construction project.